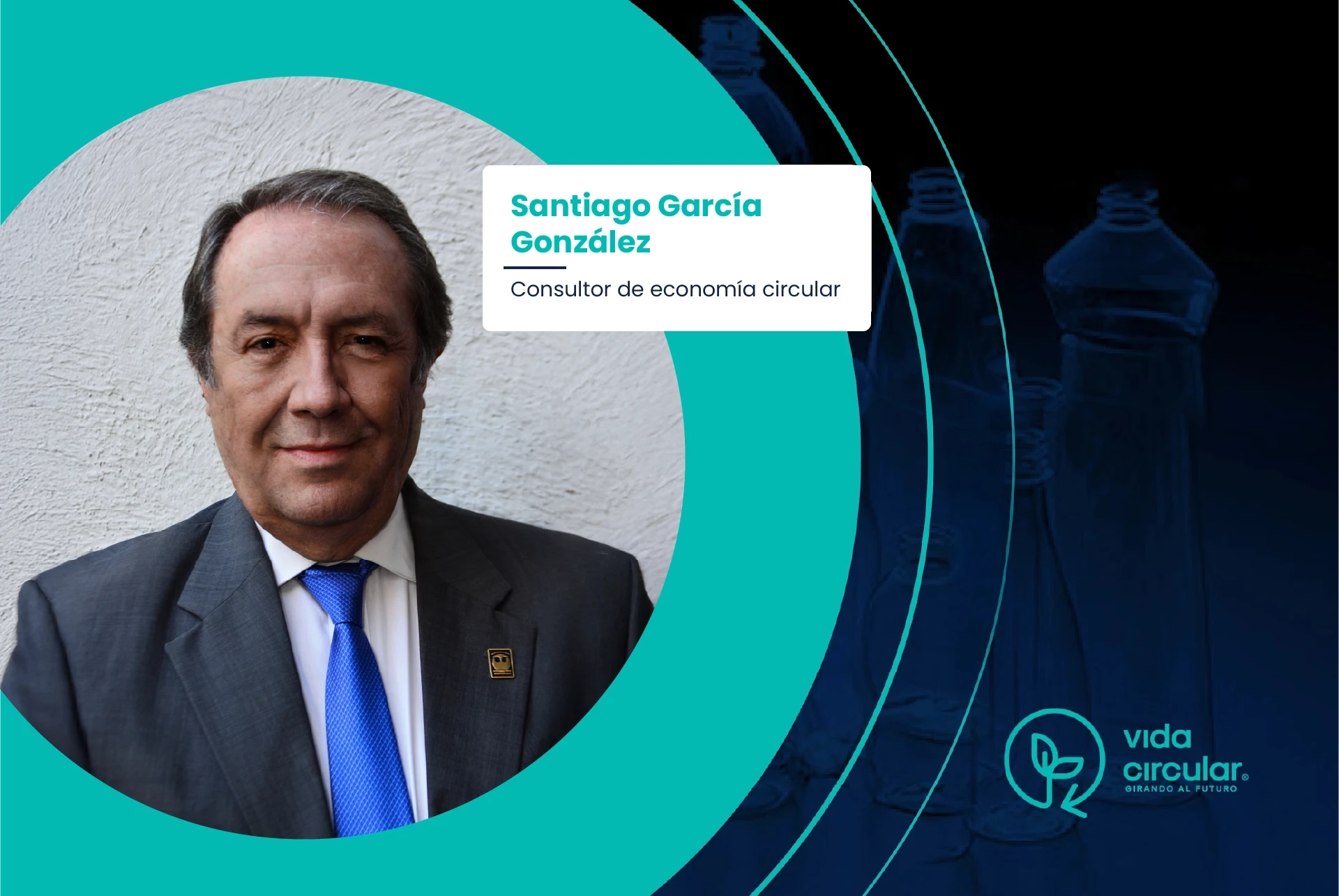
Santiago Garcia: Design guidelines for recyclability
For most plastics, the best alternative among the options in the new circular economy is recycling. Recycling plastics means huge savings in materials, energy and pollution.
There are many published figures on plastics recycling and many interpretations of them. The eternal discussion between the "glass half full and the glass half empty". But regardless of the starting point and the slope of the hill, it is essential to increase the recycling of all plastic products, especially those with a short shelf life.

Key elements for increasing recycling and eco-design
Among the elements necessary to increase the amount of recycled material and the viability of the recycling industry are the massive and selected collection, with the participation of the consumer; transportation and processing infrastructure; a stable and varied market; and as a major responsibility of the brand owner and the manufacturer of the packaging or plastic article, eco-design stands out.
Almost 10 years ago, the APR (Association of Plastics Recyclers) in the United States published the first Design Guidelines for Recyclability to provide guidance to designers, specifiers and purchasers of plastic packaging on the characteristics of packaging that make it fully recyclable in the current state of mechanical recycling technology, present certain drawbacks or, what no one wants, be considered non-recyclable.
Evolution of design guidelines and certifications
These first guides were translated into Spanish and are now included in this section of our website with the authorization of the APR. These Guidelines cover 8 base plastic materials, including PLA (poly-lactic acid), and all packaging elements such as pigments, labels, lids, etc.
But this effort has not been static. The Guides are growing, evolving and being adopted in other markets, which is fundamental in a globalized world, and have become more interactive.
The current version on the APR page https://plasticsrecycling.org/apr-design-guide allows, in a more graphic and interactive way, to navigate between the different elements of the packaging and between the different options to achieve a fully recyclable design. It also incorporates a decision tree to guide the user on the classification of their packaging and the list of products that have undergone evaluation, for which the APR endorses its use. This list is updated frequently.
Guides have also appeared in Europe, approved in the technical aspects and laboratory procedures with APR, which allow the qualification of a container with a "Design for Recycling Certification" and "Recyclability Rate Certification".
In addition to the Guidelines for bottles and rigid containers, APR has created specific ones for rigid containers other than bottles and, more importantly, for thermoformed packaging (Food Service): https://plasticsrecycling.org/beyond-bottles. The thermoformed chapter is available in Spanish on this page.

Recyclability of food packaging plastics
This section has a different format, like a table, with classification by means of a color guide. This type of packaging had been growing at a double-digit rate in several food and general purpose markets. When the pandemic came that led us to buy more things, mainly pre-packaged food, which caused an explosion in the prepared food home delivery market and caused the market growth in several of the materials to multiply.
The recycling of these packages has taken on greater urgency, in order to comply with the objectives of the Circular Economy and the General Law for the Integral Management of Waste (LGPGIR). Fortunately, there are already five plants in Mexico capable of recycling this type of packaging made of PET, and some users require a percentage of recycled material content, exclusively from these same packages, not only from PET bottles.
The recycling of thermoformed packaging presents several challenges, from handling and compaction, due to the great variety of shapes, the thinness of the wall and the difficulty of bulk handling. In the recycling process itself, advances in identification and separation equipment (sorters) have solved the problem of identifying the type of base resin, but the other stages of milling, washing, flotation, drying and separation have complications such as the generation of fines, transport through the equipment and, in general, higher process costs and higher wastage. However, recyclers have adapted quickly, the guarantee of an end market gives viability to the business and increases the amount of material available, without competing for bottles.
Also for flexible packaging, mono or multilayer, a consortium of the main European manufacturers of this type of packaging, in coordination with plastic film recyclers, have created recommendations to make these packages more recyclable in mechanical processes. These design guidelines can be consulted at: https://guidelines.ceflex.eu/guidelines/
Flexible packaging has had an important growth because they are very attractive in the store for the consumer, they represent a great saving in weight of material and savings in transportation, against the alternative of a rigid packaging. However, many times the printing and mainly the multilayer structures of various materials and adhesives, hinder or cancel the possibilities of mechanical recycling.
All these Design Guidelines were created to improve the capacity to recycle a plastic product, mainly containers and packaging, taking into account each of the elements that make up the package, through mechanical recycling processes, in the current state of technology. The Guidelines will be adapted as technology evolves.
Mechanical recycling is the most widely used, the most economically viable and the best environmental performance option. Thermal recovery and chemical recycling (or molecular recycling) options should only be complementary to mechanical recycling, for containers that cannot be adapted following the Design Guidelines. Thinking of chemical recycling as a magical option with no limits on the type or quality of feed to the process should be avoided.
Chemical recycling processes are multiple. Some simply produce fuels, others produce new molecules or monomers or treated polymer precursors. They can be a great option for plastics collected in small quantities, for plastics that suffer a lot of degradation in the mechanical process, for mixtures of plastics that are costly and difficult to separate, as well as similar cases.
I encourage all professionals involved in the design, specification, procurement and manufacture of containers, packaging and their elements to consult these Design Guidelines regularly to ensure that the plastic packaging or product they place on the market can be recycled efficiently, and that we have a viable and thriving recycling industry.
About the author:
SANTIAGO GARCÍA GONZÁLEZ Chemical Engineer from the National University of Mexico (UNAM), scholarship holder in food technology in Great Britain, worked for 10 years in the chemical and metallurgical industry at Industrias Peñoles, in Mexico and New York.
In 1989 he initiated the project of one of the first PET container manufacturing companies in Mexico, and was director of Continental PET Technologies for Latin America until 2001. In 1995 he headed the group that formed APREPET A.C., the first association of the PET container production chain, and was its first president.
From November 2002 to 2008 he served as General Manager of APREPET A.C. From 2009 to 2017 he was Senior Consultant of PCI-Wood MacKenzie of Great Britain. From August 2018 to July 2019, he was Technical Advisor of INBOPLAST. Additionally, since 2012 he has been coordinator of the Recycling Committee of Ecoce A.C.